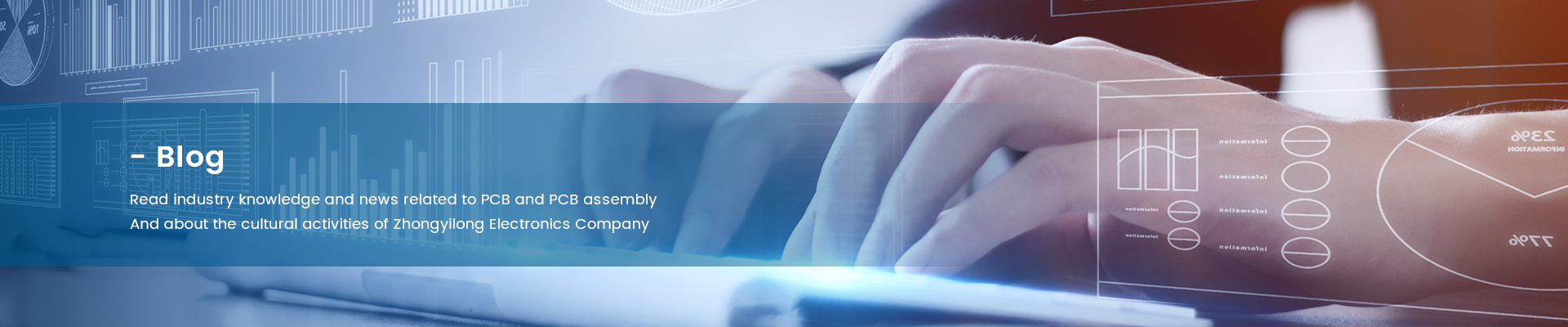
PCB Assembly Insights for Innovative Smart Pet Feeders
2025-07-25
PCB Assembly Insights for Innovative Smart Pet Feeders
Table of Contents
- 1. Introduction to Smart Pet Feeders and PCB Technology
- 2. Understanding PCB Assembly: The Backbone of Smart Devices
- 3. Key Components of Smart Pet Feeders
- 4. The Manufacturing Process of PCBA in Smart Pet Feeders
- 5. Design Considerations for PCB in Pet Feeders
- 6. Ensuring Quality Control in PCB Assembly
- 7. Emerging Trends in Smart Pet Technology
- 8. The Future of PCB Assembly in Pet Care Devices
- 9. Conclusion
- 10. FAQs
1. Introduction to Smart Pet Feeders and PCB Technology
In recent years, the pet care industry has seen a remarkable transformation, primarily due to advancements in technology. Smart pet feeders have emerged as a solution to the challenges of managing pet diets and ensuring their well-being. These innovative devices utilize advanced **PCB assembly** techniques to control feeding schedules, portion sizes, and even monitor pet health. Understanding the intricacies of PCB assembly is essential for anyone looking to innovate in this space, as it serves as the core of the technology that powers smart pet feeders.
2. Understanding PCB Assembly: The Backbone of Smart Devices
PCB assembly, or **Printed Circuit Board Assembly**, is a crucial process in the manufacturing of electronic devices. It involves the integration of various components onto a circuit board to create a functioning electronic system. For smart pet feeders, this means assembling sensors, microcontrollers, and communication modules that work together to provide seamless functionality.
What is PCB Assembly?
At its core, PCB assembly involves several steps, including:
- **Soldering**: Connecting components to the PCB using solder.
- **Placement**: Accurately placing electronic components on the board.
- **Testing**: Conducting various tests to ensure the assembled board works properly.
The Importance of PCB Quality
Quality is paramount in PCB assembly, especially for devices that interact with living beings. A malfunctioning smart feeder can lead to serious health issues for pets. Thus, manufacturers must adhere to strict quality control measures to ensure each PCB meets industry standards.
3. Key Components of Smart Pet Feeders
Every smart pet feeder is equipped with several essential components that work together to provide functionality. Understanding these components helps in designing an effective **PCBA**.
Microcontroller
The microcontroller is the brain of the smart feeder. It processes input from sensors and executes commands based on pre-programmed feeding schedules.
Sensors
Smart feeders often include sensors that monitor the food level, pet presence, and sometimes even the weight of the pet. These sensors help in automating the feeding process and provide valuable data to pet owners.
Communication Modules
Most smart feeders come with WiFi or Bluetooth modules, allowing pet owners to connect to their devices via smartphones. This connectivity enables remote feeding, monitoring, and notifications.
Power Supply
Powering the smart feeder efficiently is crucial. This can be achieved through batteries, USB power, or even solar panels, depending on the design.
4. The Manufacturing Process of PCBA in Smart Pet Feeders
The manufacturing process of PCBAs in smart pet feeders involves several stages, each critical to the overall performance of the device.
Design and Prototyping
Before mass production, a prototype is created. This allows engineers to test functionalities and make adjustments based on real-world performance.
Sourcing Components
Choosing the right components is essential. This involves finding suppliers who provide high-quality parts that meet the specifications of the smart feeder.
Assembly Line Production
Once components are sourced, they are assembled on an **assembly line**. Automated machines often handle this process, ensuring precision and speed.
Testing and Quality Assurance
After assembly, each PCB undergoes rigorous testing to ensure it functions as intended. This includes electrical testing and simulations to detect any potential failures.
5. Design Considerations for PCB in Pet Feeders
Designing a PCB for a smart pet feeder requires balancing functionality, size, and cost.
Size and Form Factor
The PCB must fit within the constraints of the feeder design while accommodating all necessary components.
Heat Management
Smart devices can generate heat, particularly during prolonged use. Proper thermal management is necessary to ensure longevity.
Durability and Reliability
Since pet feeders are often placed in various environments, PCBs must be durable and resistant to moisture, dust, and pet interactions.
6. Ensuring Quality Control in PCB Assembly
Quality control is crucial in PCB assembly, especially for devices intended for daily use by pets.
Visual Inspection
Visual inspections help identify any physical defects on the PCB before they can cause issues.
Automated Testing Systems
Automated test systems can simulate device conditions, allowing engineers to detect faults before they reach consumers.
Compliance with Standards
Ensuring that the PCBA complies with industry standards is necessary for safety and reliability. This includes certifications for environmental safety and electrical performance.
7. Emerging Trends in Smart Pet Technology
The landscape of smart pet technology is continually evolving. Keeping an eye on emerging trends can help manufacturers stay competitive.
Integration of AI
Artificial intelligence is being integrated into smart feeders to offer personalized feeding schedules based on pet behavior.
Health Monitoring Features
Newer models include health monitoring capabilities that track a pet's weight and eating habits, providing valuable insights to owners.
Eco-Friendly Solutions
Sustainability is becoming a priority, with many manufacturers exploring eco-friendly materials and energy-efficient designs.
8. The Future of PCB Assembly in Pet Care Devices
As technology progresses, the future of PCB assembly in smart pet feeders looks bright.
Advanced Manufacturing Techniques
Techniques such as 3D printing and flexible electronics may revolutionize how PCBs are designed and produced.
Increased Customization
Customization options for pet feeders will likely expand, allowing consumers to tailor devices to their specific needs.
Enhanced Connectivity
Future smart pet feeders may leverage improved connectivity options, including 5G and IoT advancements, to provide real-time updates and data analytics.
9. Conclusion
The integration of PCB assembly in innovative smart pet feeders is reshaping how we care for our furry friends. With a keen understanding of the components, manufacturing processes, and design considerations, companies can innovate and create advanced solutions that enhance pet well-being. As technology continues to evolve, so too will the opportunities for PCB assembly in pet care devices, paving the way for a brighter future for pets and their owners alike.
10. FAQs
What is a smart pet feeder?
A smart pet feeder is a device that automates pet feeding schedules and portions, often connected to a smartphone app for remote management.
How does PCB assembly work?
PCB assembly involves placing electronic components onto a printed circuit board and soldering them to create a functional electronic device.
Why is quality control important in PCB assembly?
Quality control ensures that the assembled PCB functions correctly and meets safety standards, which is crucial for devices used in pet care.
What are the benefits of using smart pet feeders?
Smart pet feeders offer convenience, allow owners to monitor their pets' eating habits remotely, and can help manage dietary needs effectively.
What future technologies might impact smart pet feeders?
Future technologies such as AI, IoT, and advanced manufacturing techniques will likely enhance the functionality and customization options of smart pet feeders.
Related News