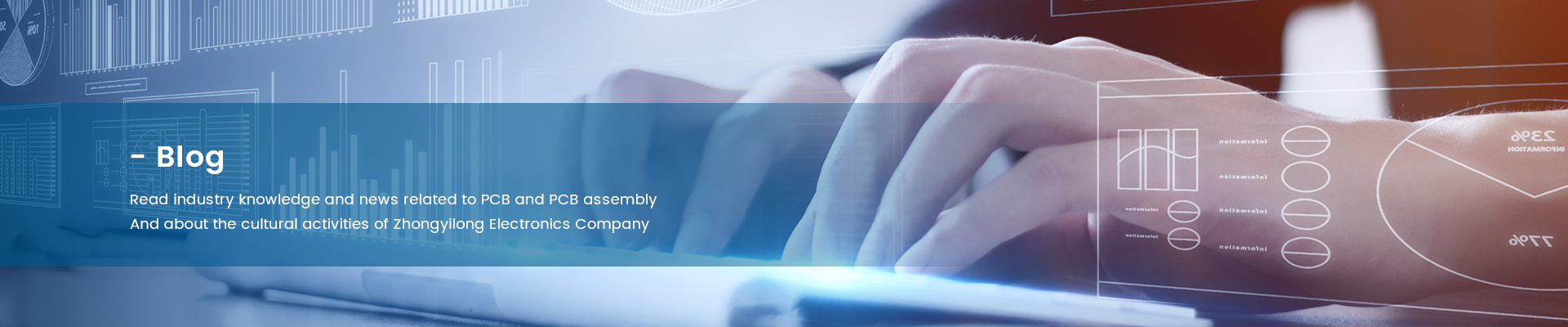
The Essential Guide to Smart Pet Feeder PCB Assembly: Innovations and Considerations
2025-07-22
The smart pet feeder industry has seen considerable growth, driven by the increasing demand for automated solutions to pet care. Central to this innovation is the PCB (Printed Circuit Board) assembly, which serves as the backbone of any electronic device, including smart feeders. Understanding the nuances of Smart Pet Feeder PCB Assembly is crucial for designers and manufacturers aiming to create efficient and reliable products.
When embarking on the PCB assembly for smart pet feeders, it is essential to consider the specific functionalities required. Features such as portion control, programmable feeding schedules, and connectivity options (like Wi-Fi or Bluetooth) necessitate a well-thought-out PCB design. Each feature may require different components, such as microcontrollers, sensors, and communication modules, all of which need to be integrated seamlessly on the PCB.
One important aspect of Smart Pet Feeder PCB Assembly is component selection. The choice of components not only affects the performance of the feeder but also its durability and power efficiency. For instance, opting for low-power microcontrollers can enhance battery life, which is especially important for feeders designed for portable use. Additionally, the integration of sensors such as weight sensors or cameras can provide real-time data about pet feeding habits, allowing for smarter feeding solutions.
The manufacturing process of PCB assembly involves several critical steps, including soldering, testing, and quality control. Soldering techniques, such as surface mount technology (SMT) or through-hole mounting, can greatly influence the efficiency and reliability of the final product. Moreover, it is essential to conduct thorough testing at various stages to ensure that the assembled PCB meets the required specifications and operates correctly under varying conditions.
Another significant consideration in Smart Pet Feeder PCB Assembly is the environmental impact. As consumers become more eco-conscious, using eco-friendly materials and processes in PCB manufacturing can provide a competitive edge. This can range from using recyclable materials in the PCB itself to adopting manufacturing practices that reduce waste and energy consumption.
In conclusion, the success of a smart pet feeder lies in its PCB assembly, which underpins its functionality and user experience. By focusing on innovative design, careful component selection, and a rigorous manufacturing process, companies can create smart pet feeders that not only meet consumer demand but also stand out in a crowded market. For those in the electronic components and PCB assembly industry, understanding these elements is key to driving growth and innovation in the smart pet feeder segment.
When embarking on the PCB assembly for smart pet feeders, it is essential to consider the specific functionalities required. Features such as portion control, programmable feeding schedules, and connectivity options (like Wi-Fi or Bluetooth) necessitate a well-thought-out PCB design. Each feature may require different components, such as microcontrollers, sensors, and communication modules, all of which need to be integrated seamlessly on the PCB.
One important aspect of Smart Pet Feeder PCB Assembly is component selection. The choice of components not only affects the performance of the feeder but also its durability and power efficiency. For instance, opting for low-power microcontrollers can enhance battery life, which is especially important for feeders designed for portable use. Additionally, the integration of sensors such as weight sensors or cameras can provide real-time data about pet feeding habits, allowing for smarter feeding solutions.
The manufacturing process of PCB assembly involves several critical steps, including soldering, testing, and quality control. Soldering techniques, such as surface mount technology (SMT) or through-hole mounting, can greatly influence the efficiency and reliability of the final product. Moreover, it is essential to conduct thorough testing at various stages to ensure that the assembled PCB meets the required specifications and operates correctly under varying conditions.
Another significant consideration in Smart Pet Feeder PCB Assembly is the environmental impact. As consumers become more eco-conscious, using eco-friendly materials and processes in PCB manufacturing can provide a competitive edge. This can range from using recyclable materials in the PCB itself to adopting manufacturing practices that reduce waste and energy consumption.
In conclusion, the success of a smart pet feeder lies in its PCB assembly, which underpins its functionality and user experience. By focusing on innovative design, careful component selection, and a rigorous manufacturing process, companies can create smart pet feeders that not only meet consumer demand but also stand out in a crowded market. For those in the electronic components and PCB assembly industry, understanding these elements is key to driving growth and innovation in the smart pet feeder segment.
Related News